The Newsroom
PABCO PRO Tip: Top 10 Sound Control Recommendations
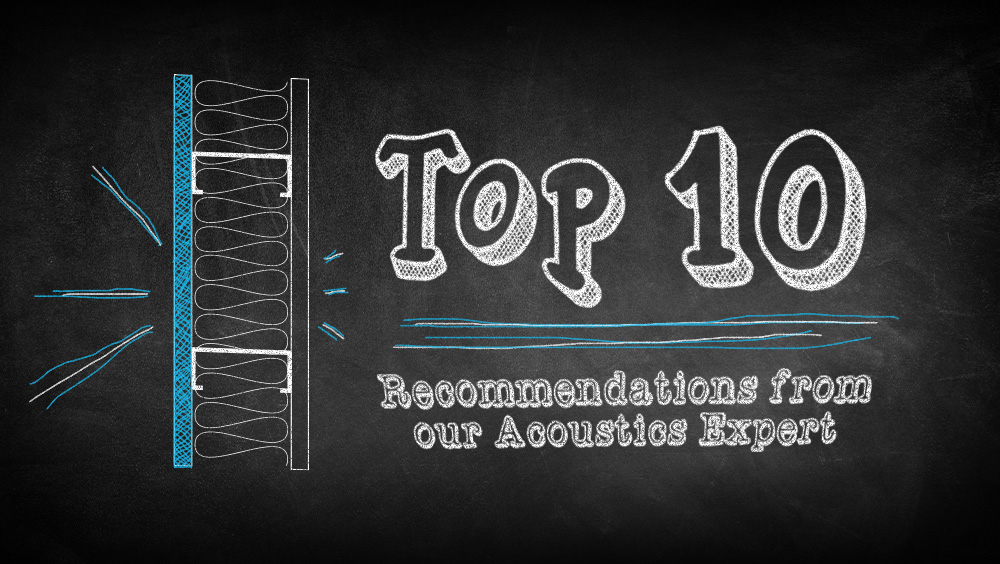
By Ben Shafer, PABCO Technical Services Manager-Acoustic Systems
- Address sound control in the design process. Money and resources have been wasted on litigation and demolition/remodeling because acoustical consultants and engineers were not brought into the design process beforehand. It pays to budget time and money to adequately address noise before the assembly is installed.
- Don’t assume. Many statements about sound isolation float around the building construction industry like “just add insulation” or “adding a layer on each side will cut the noise in half.” Most statements like these are either specific to only one type of assembly or they are downright wrong. It’s always best to thoroughly check lab test reports and evidence-based information before proceeding with a design.
- Pay attention to laboratory testing details. Be sure to look for things like panel screw spacing (attachment to framing) and frame spacing as well as mil thickness (for steel studs). Any detail could make a difference in sound isolation.
- Do some testing. Hire an engineer to investigate your building partitions for sound flanking. Standardized field sound transmission loss testing combined with sound flanking investigation (using sound intensity) is a powerful combination to know more precisely how isolated building partitions are as well as for fixing potential noise issues.
Make it airtight. Any gap in demising walls will allow sound to leak through to the other side, so make sure all potential gaps are sealed with a nonhardening sealant that won’t shrink inside the gaps or crack.
- Investigate joints. The joints between adjacent partition surfaces are notorious for allowing sound through partitions. You can reduce the risk by ensuring that designed joints are either decoupled or designed with adequate barriers to sound.
- Consider HVAC designs. Be sure to design HVAC systems so that supply and return vents branch out from a main line and into each room rather than across demising partitions.
- Treat purposeful penetrations properly. Holes in partitions are necessary from recessed lighting to electrical outlets. Be sure to design the location of these penetrations to minimize sound transmission across the assembly and treat them with appropriate barriers for sound.
- Avoid triple-leaf assemblies. It seems like an easy solution to just throw on some resilient channels and another panel onto an existing wall partition, but this is a big mistake when it comes to sound isolation. Continuous airspace is great, like the kind of airspace you find in double-stud assemblies. But when you break that airspace into multiple smaller cavities, this creates what is called the triple-leaf effect (multiple connected cavities resonating together). Treatments such as adding damped panels to the partition or removing the panels on one side to add more framing or decoupling will provide better sound isolation.
Have a multiple-angles perspective. Sound waves are not one dimensional. Sound energy finds a way through nearly all built environments. It is best to approach assembly design and implementation from multiple angles to address sound isolation rather than focusing on just one aspect of a partition design. It’s easy to get caught up in noise problems by blaming the first thing you see or notice in a design or finished construction. Look beyond the panel when there is a noise issue and also consider the connecting surfaces, the HVAC, recessed lights, unsealed seams or cracks, and other variables which may be the cause of the problem. Keep an open mind and ask questions.