The Newsroom
PABCO PRO Tip: Modifying Building Designs While Maintaining Fire Protection
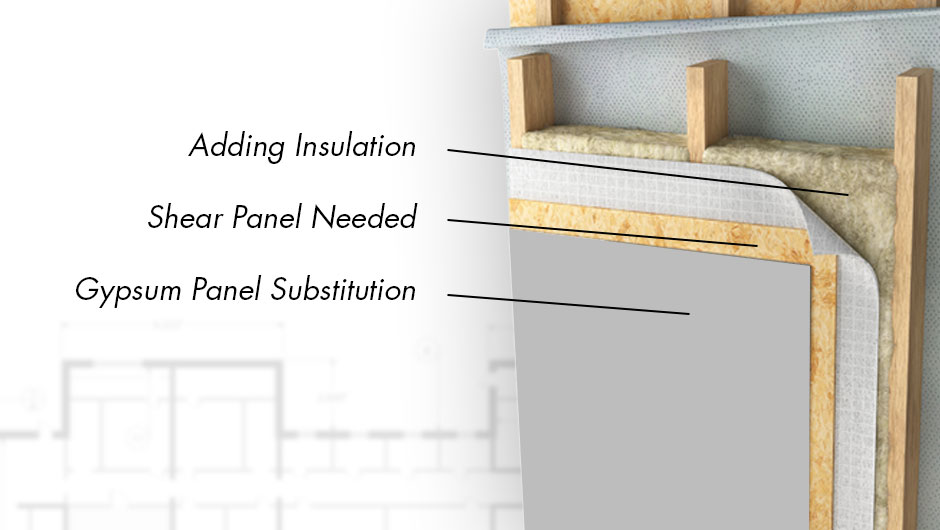
By Deborah Callaway, PABCO Manager, Technical Services
Changes to fire-resistance rated assemblies may be required or desired in certain situations. To maintain the desired fire protection, some changes can be made, some cannot, and some can be made provided modifications are also made according to the Gypsum Association and UL Solutions.
Adding Insulation
The most common change is the addition of insulation to an assembly that was fire tested without it. In wall assemblies, faced or unfaced mineral wool, glass fiber, or cellulose fiber insulation may be added to the stud cavity. The insulation must be sized to allow for a friction fit into the stud cavity. Because adding insulation may improve the acoustic performance of the wall assembly, it is one of the most common changes. If an assembly was tested with insulation, it cannot be omitted.
Care must be taken when considering the addition of insulation to a floor/ceiling or roof/ceiling assembly that was not fire tested with it. For one-hour fire-resistance rated assemblies, glass fiber insulation (either loose-fill, faced or unfaced, batt or blanket) may be added to the plenum or joist space above the gypsum panel. However, it will require an additional layer of gypsum panel of the same type and thickness, as shown in the tested design. The base layer of gypsum board must be attached with the fastener type and spacing as described in the design; it is not necessary to tape the joints of the base layer. The face layer of gypsum board must also be attached with the fastener type and spacing as described in the individual design, however the length of the fasteners must be increased by a minimum of the gypsum panel thickness of the additional layer. The joints in the finish layer must be finished as described in the design. If an assembly was tested with insulation, it cannot be omitted.
Adding Shear Panels
In regions of seismic or wind load requirements, shear panels may be added to any wall assembly when needed. They can be added as the base layer under the gypsum panels, as a face layer over the gypsum panels, or in between layers of gypsum panels. The length of the fasteners for each layer, except for the face layer, need to be increased by the thickness of the shear panel added. Fastener spacing for the gypsum panels must be as detailed in the fire design, and the spacing for the shear panels must be determined by the amount of shear required, as determined by the building codes. PABCO® has tested many wall assemblies with shear panels added. For more information, contact PABCO Technical Services. Additional information, standards, and other requirements for shear panels can be found in Section II Part 13 of the UL BXUV Guide for Fire-Resistance Ratings.
Additional Gypsum Layers
Acoustic performance of fire-resistance rated assemblies can be improved by installing additional layers of gypsum panel products. Provided the minimum layers, thickness, and type of panels required per the fire design are installed, additional layers of any thickness and type may be added to one or both sides of wall assemblies and to the face or base layer of floor/ceiling or roof/ceiling assemblies. The length of the fasteners for each layer, except for the face layer, need to be increased by the thickness of the gypsum panel(s) added.
Gypsum Panel Substitutions
The most common substitution question is, “Can I substitute 5/8” FLAME CURB® Type X for 5/8” FLAME CURB® Type C?” The answer here is a resounding, “NO!” Under no circumstance, can any thickness type X panel be substituted for any thickness type C panel because type C panels are manufactured with enhanced fire-resistance over type X. Type C panels however can be substituted for the same thickness type X panels in any fire-resistance rated assembly.
Also asked is if 1/2” gypsum panels can be substituted for 5/8” gypsum panels, or vice-versa. This one is a little tricky. Thicker panels of the same core type can be substituted, but not the other way around. For example, 5/8” FLAME CURB® Type C can be substituted for 1/2” FLAME CURB® Type C. However, 1/2” FLAME CURB® Type C cannot be substituted for 5/8” FLAME CURB® Type C. Also 5/8” FLAME CURB® Type X cannot be substituted for 1/2” FLAME CURB® Type C, nor can 1/2” FLAME CURB® Type C be substituted for 5/8” FLAME CURB® Type X.
Minimum Requirements
Some details in fire designs are listed as minimums, unless otherwise stated, and can be increased if desired. Specifically, stud thickness and depth. With increasing energy code requirements comes the need for thicker insulation materials to meet minimum regional performance. This, in turn, requires a deeper stud cavity to allow the insulation materials to perform properly or simply fit. For wood framed walls, 2×6 studs can be substituted for 2×4 studs, however, 2×4 studs cannot be substituted for 2×6 studs. For steel framing the depth of the stud can also be increased; 6” studs can be substituted for 3 5/8” studs of the same mil thickness. Again, the opposite is not true in that a shallower stud cannot be used in lieu of a deeper stud. Just as increasing the stud cavity is beneficial for insulation materials, it may also improve acoustic performance.
Minimums also exist for the mil thickness of steel framing, which can be increased without affecting fire performance. However, increasing non-load bearing studs to load bearing studs will not change the load bearing allowance of the fire-resistance rated assembly. Each fire design is designated as non-load bearing or load bearing depending on how it was tested, i.e., with or without simulated load. Typically load bearing walls are tested with minimum 33 mil steel studs, thus, 18 mil studs, or thinner, cannot be used. If a minimum acoustic performance is required for a steel studded assembly, increasing the mil thickness likely will have a negative impact, depending on other factors.
Maximum Requirements
Just as some details in fire designs are minimums, others are maximums. Stud spacing and fastener spacing to be exact. Because they are listed as maximums, they cannot be increased for any reason. While they can be decreased, doing so may have a negative impact on acoustic performance. Decreasing stud spacing will decrease the stud cavity and reducing the fastener spacing will create more contact points for the gypsum panels, and both can potentially decrease STC ratings.
For more information on this topic, contact PABCO Technical Services, 866-282-9298, techservice@pabcogypsum.com.